以下内容来源于AMLetters
金属增材制造技术为产品结构-功能一体化设计和制造带来更多的可能性,“粉床”工艺已在工业领域取得了许多系列化应用。多材料增材制造无疑是金属3D打印领域的最新前沿技术之一,此方向的技术突破将为更多高端制造领域赋能。德国Fraunhofer联合SLM Solutions研究了由两种任意组合的合金粉末的增材制造设备和工艺,并展望了多材料增材制造金属组件的前景。
01 背景介绍
近年来,增材制造凭借其独特的优势和巨大的潜力得到了加工制造领域的广泛认可。激光粉末床工艺已经在航空航天、医疗、模具、石油、核电等行业实现了规模化生产。增材制造技术使产品设计突破了传统制备工艺的限制,获得了更高的设计自由度——例如:
等应力设计的拓扑结构可以根据零件承受的负载进行优化,优化后的零件大多为异形结构,传统工艺面临无法加工和成本高昂等问题,而复杂结构正是增材制造的强项。
模具行业的随形水路结构,之前同样受限于传统的加工手段,而目前,增材制造在模具行业已经是非常普遍的应用,散热更加高效均匀的随形水路模具为整个注塑行业注入了新的活力,研发和生产效率均获得大幅度提升。
航空航天领域的案例更是不胜枚举,从飞机、卫星、导弹、载人飞船到火箭,如今的航空航天领域的产品,背后都有增材制造的身影。然而,到目前为止,所有这些产品都是由单一的材料制成的。
金属增材制造的规模化应用大多还在高端制造领域,高端制造领域的研发资金相对雄厚,对产品性能的提高有不懈的追求。但并不是说他们不会算经济账。大量资金投入的背后逻辑其实很简单,制造的总零件数量少了100倍,开发速度快了10倍,这就是增材制造带来的改天换地的能量。我们不能局限于某个加工制造的环节来论断某种工艺的优劣、成本的高低,而应该从产品的全寿命周期来考量投资回报率。使用增材制造技术加工的某款产品在其全寿命使用期间节省的费用可能会比因引入增材技术而增加的设计和制造成本高得多。通过常规的铣削和钻削加工一个阀块虽然成本较低,但是通过面向增材制造设计(DfAM)进行内部流道优化并制造的产品能够获得更多的效益(虽然设计和制造成本增加了)。
图1 镍基和铜基合金的燃烧室部件(弗劳恩霍夫IGCV)
ISO/ASTM 52912定义,多材料组件是指至少有两种不同性能的材料紧密结合在一起的零件。实际上,大多数的LPBF设备都可以实现二维多材料打印,即材料在成形方向上发生连续变化(Z轴方向的梯度材料)。方法也很简单:
将“材料1”添加并成形到所需高度,然后清除剩余的材料1粉末,如果有必要,成形舱中的保护气体和其它环境参数做相应调整,以适应“材料2”的铺粉和激光成形。在这个清粉和工艺参数调整之后,以已成形的材料1部件作为基体,继续使用材料2进行增材制造。
综上所述,在典型的LPBF设备上,采用上述方法制造二维多材料零件虽然耗时较多(手动更换材料),但毕竟还是可行的。但对于三维多材料组件的制造,这种方法就行不通了,因为两种材料可能须同时存在于一薄层中,即三维多材料组件的特征是两种或以上的材料可以随机分布在零件的任意位置。
02 从单材料到三维多材料打印
采用LPBF生产三维多材料零件,需要提高常规LPBF设备在软件和硬件两方面的能力,以适应如图2所示的典型工艺过程。
图2 三维多材料打印的典型工艺过程
I 2-1 前处理
首先,零件多材料的分布需要由设计师来定义。这可以通过设计师自己的专业知识或使用模拟工具来实现。一旦确定了所需的材料分布方式,就需要为增材制造过程生成零件的三个子模型,如图3所示(由工具钢(1.2709)和铜合金(CuCr1Zr)两种材料制造的零件),对于每个材料需要设计一个单独的子模型,以便确定合适的材料过渡方式。
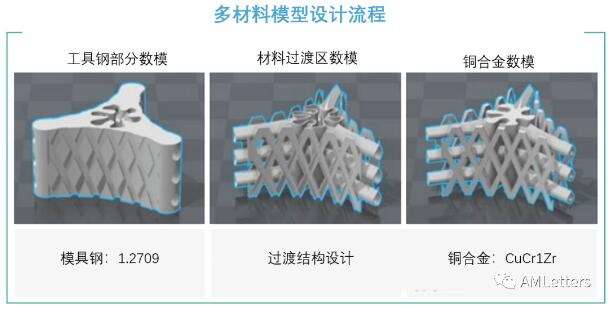
图3 基于LPBF工艺的三个数据子模型,分别是:工具钢部分数模、材料过渡区数模和铜合金数模
除了为每种材料生成子模型之外,还有第三个模型描述材料过渡区的几何特征。对于每一个子模型,为了确保各部分材料具有足够的成形质量,通常需要对每一材料制定相应的工艺参数。不同材料的粉末性能、导电性和激光吸收率等方面存在差异,为了获得较高致密度和无裂纹的零件,不同区域的激光功率、扫描速度和扫描距离会有所不同。图4为工具钢(1.2709)和铜合金(CuCr1Zr)过渡区结合方式示意图。
图4 材料过渡策略;测试样品;参数过渡
I 2-2 LPBF多材料增材工艺的流程
多材料LPBF工艺的最大挑战是实现多材料的铺粉。典型的铺粉机制不支持在一个成形舱内使用两种粉末材料。由于这个原因,常规LPBF设备的软件和硬件都需要改进,以便具备多粉末材料的铺粉功能。
图5是位于德国Fraunhofer IGCV实验室与SLM Solutions公司定制开发的SLM280 2.0多材料金属增材设备的成形腔内视图,该设备可以成形三维多材料零件。这台设备的多材料增材原理由Fraunhofer IGCV实验室开发。
图5 SLM280 2.0 设备内部的多材料铺粉器结构
简而言之,双舱铺粉器在一次成形零件中提供两种粉末的按需铺粉。此外,铺粉轴上还装有吸粉装置,该装置能够清除未熔化粉末。因此,多材料重复循环应遵循以下步骤:
1) 根据材料A的子模型数模,将材料A铺覆在第n层上并进行选择性激光成形;
2) 未熔化的材料A粉末由铺粉轴上的吸粉装置去除;
3) 将材料B铺覆在第n层并根据其子模型数模进行激光成形,未熔化的材料B粉末留在成形舱中;
4) 成形平台降低一个层高度,对第n+1层重复上述步骤。
按照步骤1-4中描述的流程,材料B留在舱室中,而材料A不断被吸粉装置清除。
I 2-3 后处理
多材料LPBF后处理最大的挑战是粉末混合物的分离。在步骤1-4所述的铺粉过程中,两种粉末材料的混合是不可避免的。这是因为第2步使用吸粉装置清除未熔化的物料A粉末难以完全去除。
理论上讲,只除去一层粉末就足够了。这将从成形舱中完全移除材料A,只剩下材料B。同时,吸粉装置中只剩下材料A。然而,目前的技术水平不可能达到如此精确地去除粉末层。粉末的粒度分布和由此产生的颗粒团聚,以及吸粉装置的差异性和精度都有限制,这意味着在清除粉末时通常会吸入三层或更多层粉末,以避免成形过程中的污染。
因此,Fraunhofer还研究了使粉末混合物循环利用的一般方法,如图6所示。
图6 混合粉末的分离、重复使用的主要原则(筛分、磁性分离、重介质分离、重力分离、静电分离、浮选分离)
混合粉的分离方法是依据各粉末材料的特性差异来选择。例如,如果一种粉末材料具有磁性,而另一种粉末材料没有磁性,则可以采用磁性分离。如果是粒径不同且粒度分布无重叠的粉末,则可以使用筛分法来分离。此外,其他物理原理也有被用来分离混合粉末,但它们的适用性明显低于磁选或筛分。为了能够重复使用粉末,实际上并不需要实现100%分离,所需材料的纯度水平依赖于材料的组合。这也是一个颠覆常规认知的经典论述。
03 多材料增材的工业潜力和案例
多材料零件能够根据零件使用环境需求,利用各种材料性能的最佳组合来实现零件功能。例如,耐磨耐热钢可以与导热性能良好的铜合金结合,用于大口径发动机。图7显示了德国Fraunhofer IGCV和MAN Energy Solutions SE联合研究的喷油嘴案例。
图7 基于LPBF多材料打印的案例,大口径发动机喷油嘴;优势:1)提高高应力区域的热传导效率;2)提高燃油喷嘴的耐高温能力;3)提高发动机的性能
该零件在高应力区域工具钢材料的内部,采用高导热性的铜芯来快速传导喷油嘴的热量,从而提高发动机性能。图7所示的组件是按照上述设计思想进行多材料增材制造的。
图8显示了由两种不同成分的钢组成的齿轮的截面。步骤1-4描述了这个过程。在这种情况下,材料2是粉末混合物,并在齿轮的外围区域沉积。在材料2粉末中,通过添加碳元素提高了钢的碳含量。这导致在部件内部(材料1,H13,1.2344)的C含量约0.2 wt.%,而在部件外部边界处的C含量约0.8wt%。在激光成形过程中存在循环加热,由于碳的扩散导致两个区域之间形成了C浓度梯度。LPBF工艺允许有选择地设置和调整边缘层的厚度。这样就能在齿侧产生最佳硬度剖面,并同时在齿根产生具备最优承载能力的材料成分梯度。此外,同样的工艺可以用于制造组件内部的加强筋(图8b),这使得传统的常规表面硬化处理不再是必要选项。只需加热和淬火即可产生完整的马氏体表面层。上述增材制造工艺提供了一种非常具备有潜力的齿轮制造方式。
图8 基于LPBF工艺的两种钢铁增材的工业齿轮,优势:1按需定制材料性能,拓展产品设计自由;2提高零件耐磨性和力学性能; 案例:左)在齿侧和齿根处,不同的表面硬化深度(CHD),以获得最佳承载能力;右)具有内部加强筋的齿
图9所示的燃烧室是一个来自航天工业的例子。燃烧室面临高热负荷,但也需要尽可能轻。燃烧室的性能越好,火箭性能就越好,产生同样推力的推进器质量越小,就能向客户提供更多的有效运输载荷。因此,增加的火箭制造成本可能会因携带更多载荷产生的效益而被抵消。因此,航天是增材制造的核心应用领域之一,特别是多材料增材制造。针对多材料增材制造的燃烧室,镍基合金作为腔体的耐热基底,而内部铜基区域能提高组件的热传导能力。
图9 火箭发动机中的镍铜混合材料燃料室
然而,本文中所示的组件并不能完全描述多材料增材制造组件的潜力。还有很多值得开发的领域,例如:
对于注射成型应用,耐磨工具钢可以与具备良好的导热性铜合金结合,显著减少生产高长径比的塑料零件的时间。
铝和铜合金的结合为也将为电机制造带来新机会。此外,结合钛合金和钽的优点可以提高人工牙齿的性能。
综上所述,目前多材料增材制造工艺已经相对成熟,某些材料配对(如铜和钢)的技术储备已足以开展工业应用,这是因为铜和钢两种材料的增材制造工艺成熟。更重要的是,这两种材料在堆积过程中产生的混合粉末,可以利用磁选进行分离,分离纯度几乎达到100%。与钢铜合金组合形成鲜明对比的是,在目前的技术下,多材料增材还很难使用各方面特征非常相似的材料组合(如密度,磁化率,粒度分布)。因为在这种情况下,混合粉末分离是非常困难的,而粉末的重复使用通常被认为是增材制造适用性的关键标准。
以上文章来源于AMLetters
|